Sustainable Liquid Flexible Packaging Manufacturer
ZACROS is committed to making our society more sustainable by creating innovative packaging solutions. Specializing solely in liquid applications, Zacros America manufactures a wide range of sustainable flexible packaging options up to 20L. We support customers switching from rigid packaging by providing support from material selections to finding filling partners.
Product Offerings
Functional and Sustainable Liquid Packaging
Need Tips for Choosing the Right Liquid Packaging?
Download the guide to help you understand different liquid packaging options and determine the right packaging for you.
Liquid Packaging Insights
Think Beyond Packaging
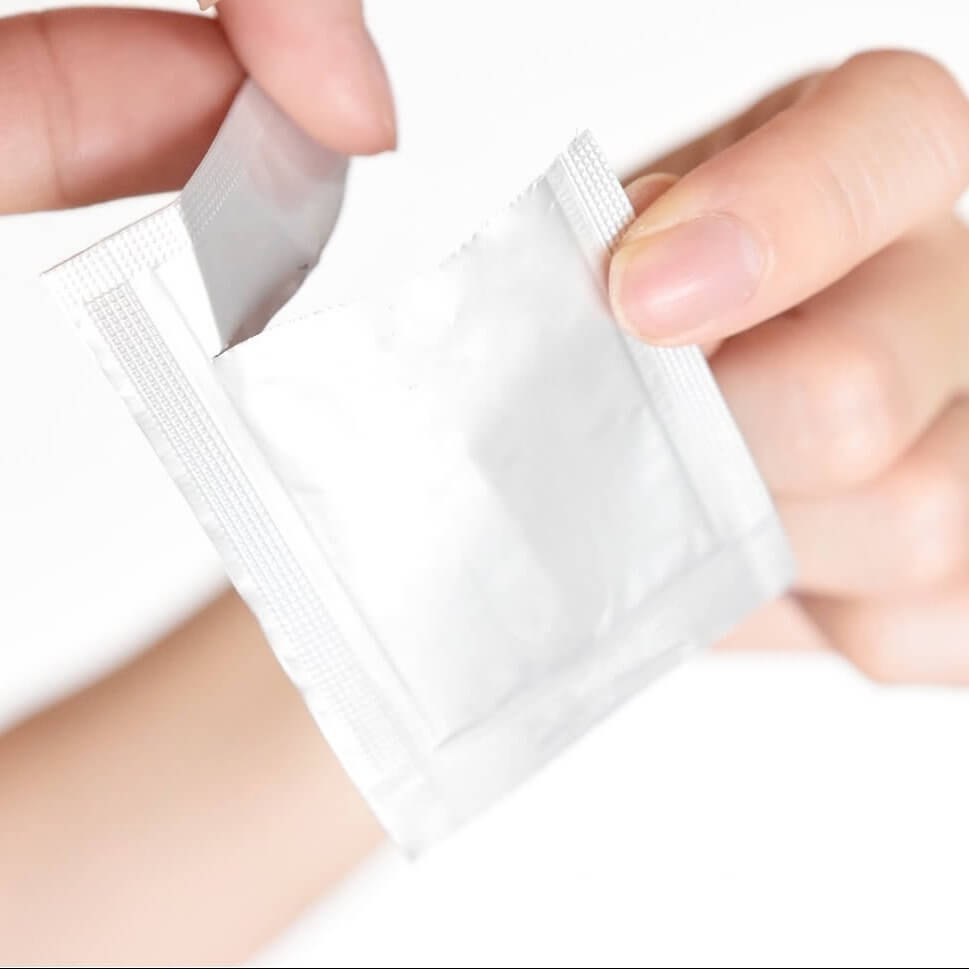
Unveiling the Power of Cosmetic Sample Sachet Packaging: A Closer Look
Cosmetic brands often use sachet packaging for their products to make the first impressions on potential customers. Whether… Read More
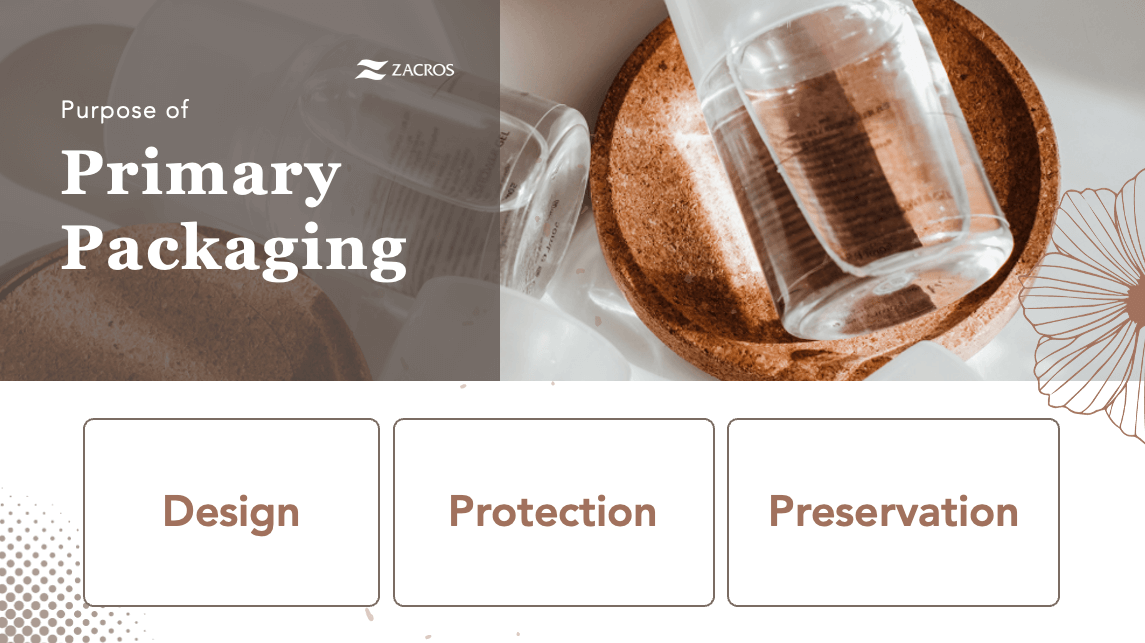
The Science Behind Cosmetics Flexible Packaging and Preservation
Packaging plays an essential role in cosmetics. Even though flexible packaging is growing in the cosmetics industry, most beauty… Read More
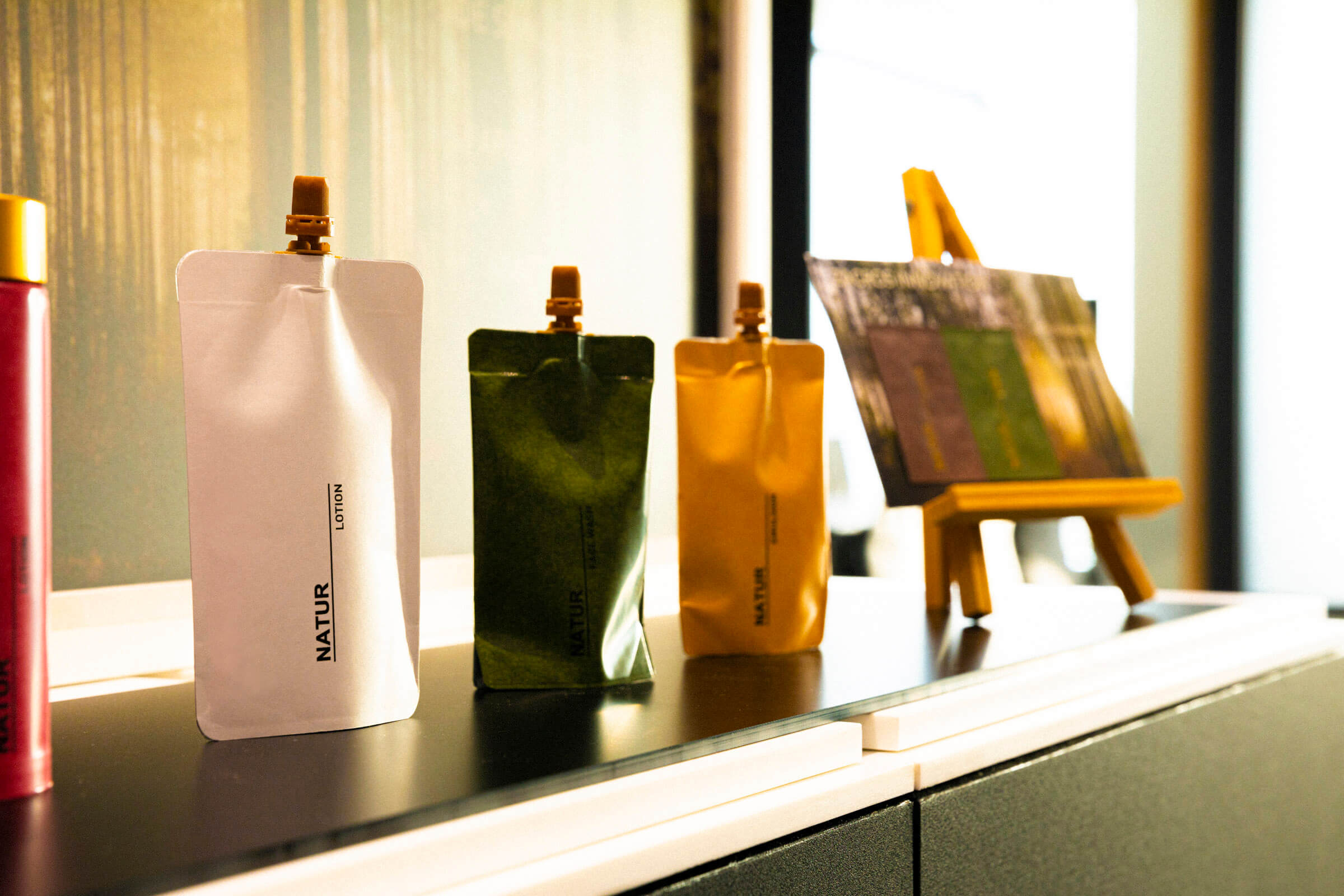
Key Considerations for Switching to Flexible Packaging in Beauty and P...
As the packaging landscape undergoes a major shift towards sustainability, we are excited to bring you insights into the flexible… Read More
Think Beyond Packaging
Our goal is to go beyond customers’ expectations with our innovation to provide liquid flexible packaging to meet their needs.
Get started on your project with our experts
Even if you don’t know where to start, don’t worry. We can help you from the start with our extensive experience in liquid flexible packaging.
Contact Us